Lubrication Oil System Checklist
It helps to have a plan when designing, re-designing, or modifying a lubrication system. Here's what we look for to improve performance and limit problems. Details below, click to jump!
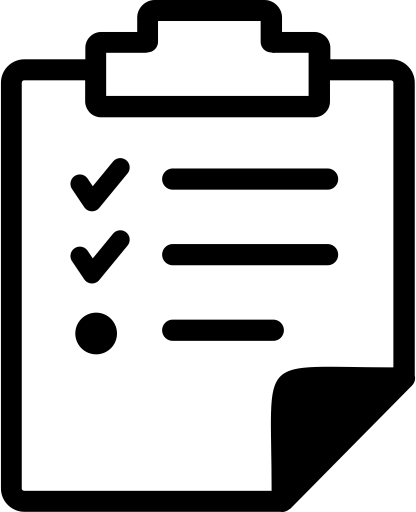
1. Lubricant has the right viscosity
Oils need to be thin enough to flow in high-speed systems, but thick enough to provide a cushion. Based on the speed and temperature of your machine, you can calculate the right viscosity
2. Sufficient Viscosity Index for temperature range
If your equipment experiences a wide temperature range, you may need to a higher Viscosity Index to make sure it doesn't thin out too much when hot
3. Pour Point low enough
Cold oil doesn't flow well. The Pour Point should be at least 5ÂșC below the expected minimum ambient temperature
4. Flash Point high enough
Hot oil might catch fire. The Flash Point should be above the highest expected operating temperature
5. The right additives for the job
Extreme Pressure (EP) additives help with high load or shock in the system, while Rust & Oxidation (R&O) additives offer protection against corrosion
Lubrication is more than just the oil, it often includes a support system to make sure clean, cool oil gets to where it needs to be (and not where it shouldn't be!)
6. Materials are compatible with oil
Your choice of oil should be compatible with everything it touches, includinig: seals, O-rings, piping, hoses, paint, sight gauge, sealant, etc. Some oils aggressively attack copper or bronze, and should be avoided when those metals are present.
7. Compatible with previous oils
If you switch oil types, the old oil should be compatible with the new, or properly and thoroughly flushed out. This is most important when switching between mineral oil and polyalkylene glycol (PAG) based oils.
8. Sight glass or level management
Being able to monitor the oil level will help identify leaks and know when it's time to add more oil to the system
9. Oil is sufficiently clean
Solid particles can get into oil during manufacturing, transport, or operation. These particles can block lines or increase wear on the equipment. Proper filtration keeps these particles out of your machine.
10. Additives are compatible with filter
Most oil additives are liquid, but some can be solid. If performance additives are necessary to the process it's important they don't get caught up in the filter.
11. Minimal air entrainment
Pumping and circulating oil can introduce air to the liquid. This air reduces the amount of oil that actually helps lubricate the system. Increasing your sump size can give more time for air to escape before it's recirculated. A volume equivalent to 1-3 minutes of flow is recommended.
12. Foaming is limited or mitigated
Entrained air can also lead to foaming in the oil. Foam-inhibitors (often silicone-based) can reduce the volume of foam
13. Stable against oxidation and temperature
As temperature increases so does the risk of degradation of the oil or its additives. Areas with high ambient or operating temperatures should consider oils with enhanced protection against heat.
14. Oil can be contained in a leak
If your oil system leaks, where does it go? Putting a tray or berm underneath your equipment can prevent oil from leaching into the environment, especially important if you store equipment outside! The recommended containment volume is at least 1.5x the maximum volume of your oil system.